Managers know you can't change what you don't understand. When it comes to operationalizing your safety culture, you need to understand the issues by collecting and analyzing data to assess your organization's current safety status. As discussed in the first blog in this series, using the U.S. military's Intelligence Framework can funnel the correct data to the right audience and highlight trouble spots to decision-makers. Then, you can use the data to plan effective mitigation programs.
Accidents Don't "Just Happen"
While workplace accidents can seem random, they often result from overlooked or misunderstood safety issues. Analyzing updated, accurate data on safety incidents can clarify the causes of accidents and their impact.
Typically, the three factors of work environment, job design, and people contribute to most workplace injuries. When planning your employee safety program, you'll want to analyze injury incidents through these three lenses to determine their root causes, then include services that address them.
- Work Environment/Set-up: When an employee gets injured, check if other workers have also had this problem. If so, the work environment probably contributed to the injury and may need adjusting. An ergonomic assessment could suggest ways to modify the work set-up to perform the job more safely.
- Job Design: The hazardous conditions of many jobs' designs can lead to cumulative trauma disorders such as carpal tunnel syndrome. Other jobs may involve strenuous lifting or twisting in awkward positions, resulting in chronic musculoskeletal injuries. Redesigning job activities can minimize the risk of these injuries.
- People: Occasionally, the employee's injury can be traced back to hiring the wrong person for the role. To avoid this, plan to use validated and updated Functional Job Descriptions and post-hire employee testing to screen people from taking jobs inappropriate for their abilities.
Data-Driven Planning
After identifying which factors undermine employee safety, you can use the data to plan programs and set measurable goals at all three operational levels.
- Strategic – At this level, senior decision-makers approve long-term actions and investments that strengthen the organization's total health culture. For example, suppose the data shows workers are not getting treatment for minor strains that later become debilitating, or the level of absenteeism is higher than average in their industry. The strategic investment may be an investment in an overall Total Wellness Program for the company.
- Operational – The Operational level focuses on daily activities and work practices to enhance worker safety. Suppose the data shows that two separate sites (distribution centers or plants) have a high rate of injuries. In that case, the company may consider starting an onsite PT program to deliver prompt, convenient treatment and train workers to perform their jobs more ergonomically correctly. If data shows that some employees can't perform the work activities safely, that could emphasize the need to overhaul job descriptions and improve employee screening. These activities become part of an overall wellness program. Ideally, initiatives at the operational level roll up into the strategic initiative of Total Wellness.
- Tactical – It's at the Tactical level where you define how strategic directives are implemented. Tactics to strengthen your safety culture might include having onsite PTs deliver regular employee exercise programs or perform monthly ergonomic assessments of the work environment.
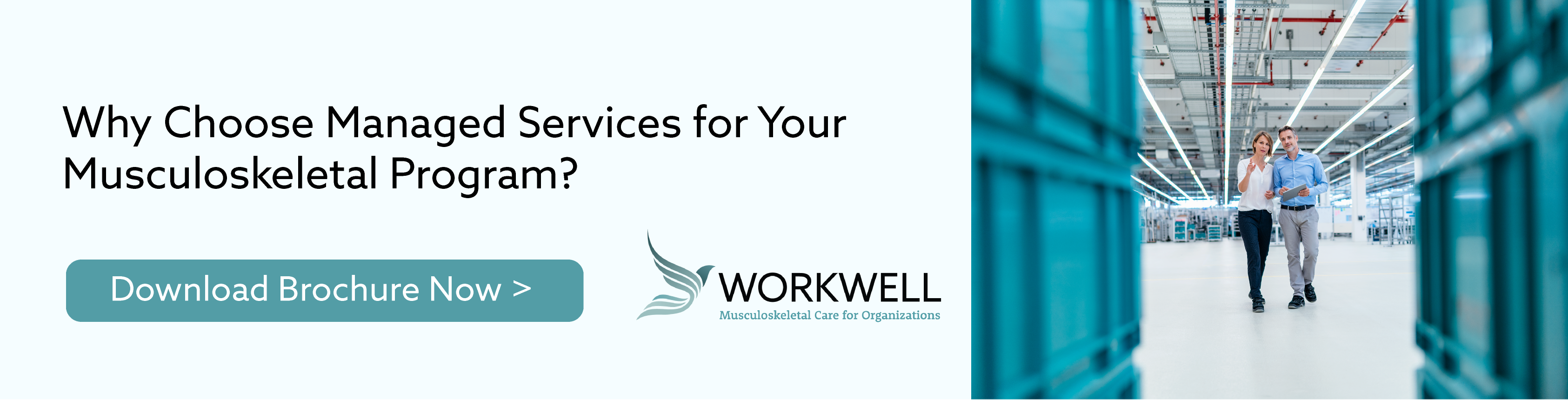